Revolutionizing Manufacturing: The Power of Rapid 3D Prototyping
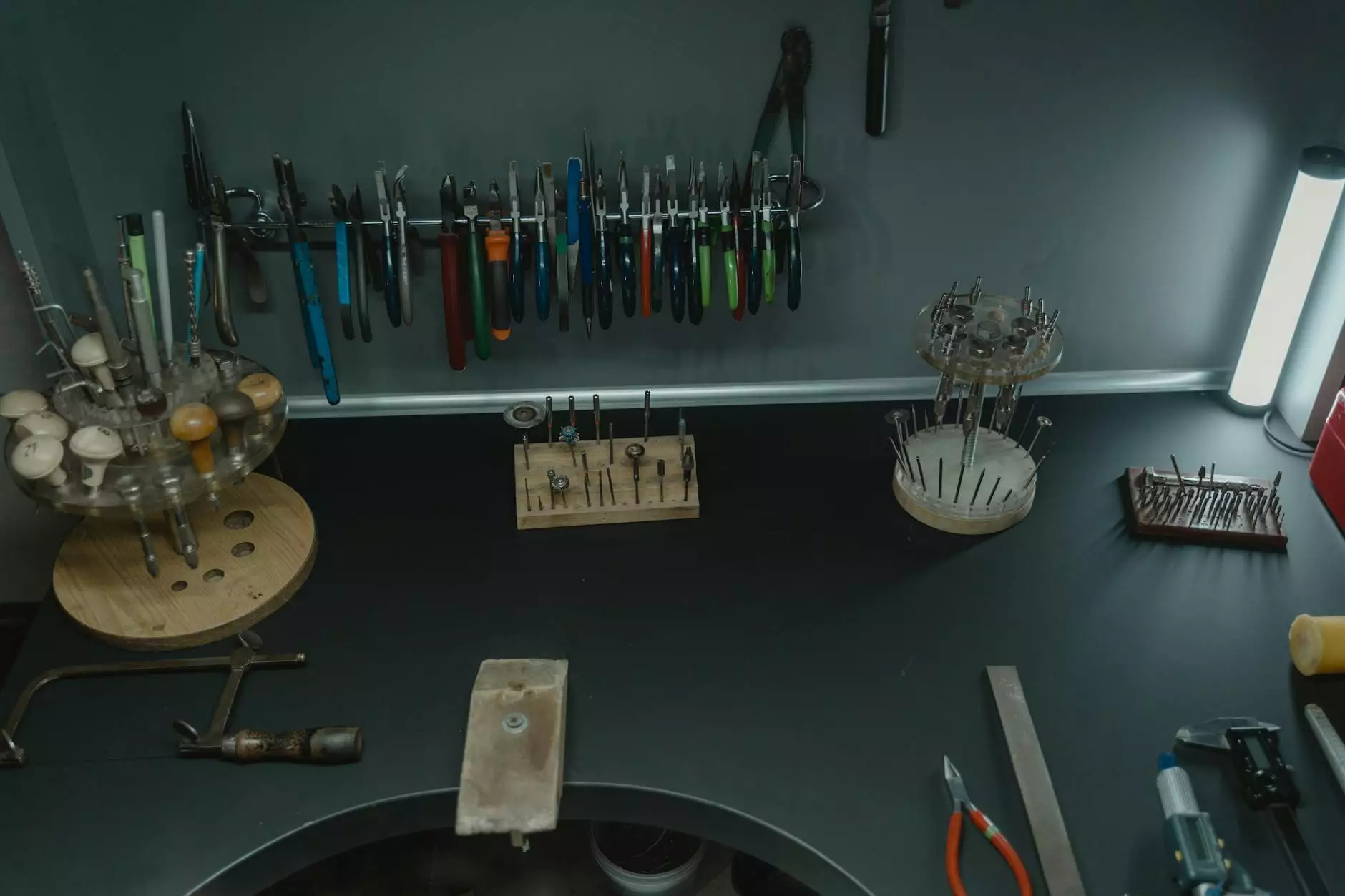
In today's fast-paced industrial landscape, businesses are constantly seeking ways to innovate and improve their manufacturing processes. One technological advancement that has made a significant impact is rapid 3D prototyping. This technique has transformed how companies approach product development, minimizing lead times, reducing costs, and enhancing overall quality. In this article, we will delve deep into the world of rapid 3D prototyping, its benefits, applications in metal fabrication, and how it is reshaping the future of manufacturing.
Understanding Rapid 3D Prototyping
Rapid 3D prototyping refers to the process of quickly creating a physical model of a product using three-dimensional computer-aided design (CAD) data. The prototyping process typically employs various additive manufacturing technologies, enabling the production of parts swiftly and with remarkable accuracy. Through a combination of techniques like 3D printing, CNC machining, and stereolithography, manufacturers can produce functional prototypes that closely resemble the final product.
Key Technologies Behind Rapid 3D Prototyping
- Fused Deposition Modeling (FDM): A popular method that works by extruding thermoplastic materials layer by layer.
- Stereolithography (SLA): Utilizes a laser to solidify liquid resin, producing high-resolution models.
- Selective Laser Sintering (SLS): Fuses powdered materials using a laser, allowing for complex geometries and durability.
- Digital Light Processing (DLP): Similar to SLA but uses a digital light projector to cure resin, enabling faster production times.
The Benefits of Rapid 3D Prototyping
The benefits of rapid 3D prototyping are vast, especially in the metal fabrication sector. Some notable advantages include:
1. Reduced Time to Market
In an industry where speed can dictate success, rapid prototyping allows companies to develop new products much faster than traditional methods. Prototypes that once took weeks or even months to create can now be produced in days or hours.
2. Cost Efficiency
By minimizing waste and utilizing resources effectively, businesses can significantly lower their production costs. Early-stage prototyping helps identify design flaws before mass production, saving time and material costs.
3. Enhanced Design Flexibility
The ability to quickly iterate on designs means that manufacturers can explore multiple concepts simultaneously. This flexibility promotes innovation and encourages creative thinking among design teams.
4. Improved Collaboration
Prototypes facilitate better communication between engineering, design, and marketing teams. Physical models serve as a common reference point, ensuring everyone is aligned and reducing miscommunication.
5. Higher Quality Products
Rapid prototyping allows for extensive testing and refinement of products before they go into full-scale production. As a result, companies can launch products that meet consumer expectations and industry standards.
Applications of Rapid 3D Prototyping in Metal Fabrication
Metal fabrication is an area where rapid 3D prototyping shines bright, as the demand for precision and durability is paramount.
1. Creating Complex Geometries
With traditional fabrication methods, producing intricate designs can be challenging. However, additive manufacturing techniques enable the creation of complex geometries that would be impossible or extremely costly to achieve using conventional methods.
2. Functional Testing
Metal prototypes can be used for functional testing and validation. This crucial step ensures that the product meets all necessary specifications and can withstand real-world conditions.
3. Custom and Low-Volume Production
Rapid prototyping is particularly beneficial for custom parts and low-volume production runs. Manufacturers can respond quickly to niche market demands without the need for expensive tooling.
4. Design Validation
Before committing to a large production run, companies can create prototypes to validate designs. This process helps ensure that products perform as intended and meet customer requirements.
Challenges and Considerations in Rapid 3D Prototyping
While rapid 3D prototyping offers numerous benefits, it is essential to be aware of the challenges that may arise:
1. Material Limitations
Not all materials are suitable for all prototyping methods. Understanding material properties and selecting the right one for the intended application is crucial.
2. Post-Processing Needs
Many rapid prototyping methods require post-processing steps such as sanding, painting, or sealing to achieve optimal surface finishes. This can add time and costs to the overall process.
3. Quality Control
Ensuring consistent quality across batches remains a challenge. Implementing robust quality control measures is necessary to maintain high standards in the production process.
Future Trends in Rapid 3D Prototyping
The future of rapid 3D prototyping is bright, with several trends on the horizon that promise to further transform the manufacturing landscape:
1. Integration with Artificial Intelligence
AI can enhance design software, optimize print processes, and predict potential defects, making rapid prototyping even more efficient and effective.
2. Hybrid Manufacturing Models
An increasing trend is the adoption of hybrid models that combine traditional manufacturing methods with additive techniques. This approach allows businesses to maximize efficiencies and reduce costs.
3. Sustainable Practices
With the rise of eco-conscious consumerism, there is a growing emphasis on sustainable materials and practices in rapid prototyping. Companies are exploring biodegradable materials and recycling techniques to reduce their environmental impact.
4. Expansion of Material Range
As technology advances, the range of materials available for 3D printing is expanding. This will lead to more versatile applications across various industries, including metals, ceramics, and even biological materials.
How DeepMould.net is Leading the Charge
At the forefront of this revolution is DeepMould.net, a leader in the metal fabrication industry specializing in rapid prototyping. Through innovative processes and state-of-the-art technology, DeepMould.net has established itself as a premier provider of high-quality, custom solutions for a variety of industries, including automotive, aerospace, and consumer goods.
Innovative Solutions
DeepMould.net employs cutting-edge technology to achieve precision and efficiency in all their projects. Their commitment to using the latest advancements in rapid 3D prototyping allows them to deliver exceptional results, meeting the unique needs of each client.
Customer-Centric Approach
Understanding that every project is unique, DeepMould.net takes a customer-centric approach, offering personalized services that cater to specific requirements. Their expert team collaborates closely with clients, ensuring that every prototype aligns with their vision.
Commitment to Quality
Quality is the cornerstone of DeepMould.net's philosophy. Their rigorous quality control measures ensure that each prototype meets the highest standards, providing clients with peace of mind as they move forward with production.
Conclusion
As industries continue to evolve, the significance of rapid 3D prototyping will only grow. Its ability to accelerate product development, reduce costs, and promote innovation makes it a vital tool in the manufacturing arsenal. Businesses like DeepMould.net are not just keeping pace with these advancements but are leading the charge into a future defined by efficiency and quality.
By investing in rapid prototyping technologies, companies can stay ahead of the competition, cater to dynamic market demands, and unleash their full creative potential. The question is no longer whether to adopt rapid prototyping, but how quickly can your business integrate such technologies to remain relevant in a rapidly changing landscape?